Spis treści
Co to jest moment obrotowy i jak się go mierzy?
Moment obrotowy to siła działająca na określony element, która inicjuje obrót obiektu wokół osi. To istotna miara, pozwalająca ocenić, jak efektywnie siła generuje ruch rotacyjny. Mierzy się go w niutonometrów (Nm), a dokładne pomiary są kluczowe dla zapewnienia, że dokręcanie elementów, takich jak:
- śruby,
- nakrętki.
Do precyzyjnych zastosowań służą klucze dynamometryczne, które umożliwiają dokładne ustawienie siły dokręcania. Właściwe korzystanie z tych narzędzi zapobiega uszkodzeniom mechanizmów, które mogą wystąpić, gdy moment obrotowy jest zbyt wysoki lub zbyt niski. W praktyce obliczanie momentu obrotowego uwzględnia zarówno siłę, jak i długość ramienia, co podkreśla znaczenie dokładnych pomiarów w inżynierii oraz mechanice. Dzięki tym pomiarom można minimalizować ryzyko błędów podczas montażu, co jest niezbędne dla trwałości oraz bezpieczeństwa wszelkich konstrukcji.
Jak przelicza się moment dokręcania w Nm?
Aby przeliczyć moment dokręcania z niutonometrów (Nm) na inne jednostki, wystarczy skorzystać z kilku prostych równań. Na przykład, jeden niutonometr odpowiada:
- 0,1 kGm,
- 0,74 lb/ft.
Kiedy posługujemy się kluczem dynamometrycznym, niezwykle istotne jest, aby ustawić odpowiednią wartość momentu. To bezpośrednio przekłada się na jakość połączeń oraz bezpieczeństwo użytkowania takich elementów jak śruby i nakrętki. Warto również wspomnieć, że istnieją online kalkulatory momentu obrotowego, które znacznie przyspieszają proces przeliczenia jednostek. Dzięki nim praca staje się dużo prostsza. Znajomość tych przeliczników pozwala na właściwy dobór siły dokręcania, co z kolei zapobiega uszkodzeniom złącz oraz zapewnia ich poprawne funkcjonowanie. Nie zapominajmy także o tarciu, które wpływa na dokładność dokręcania.
Co oznacza 90 stopni w kontekście momentu dokręcania?
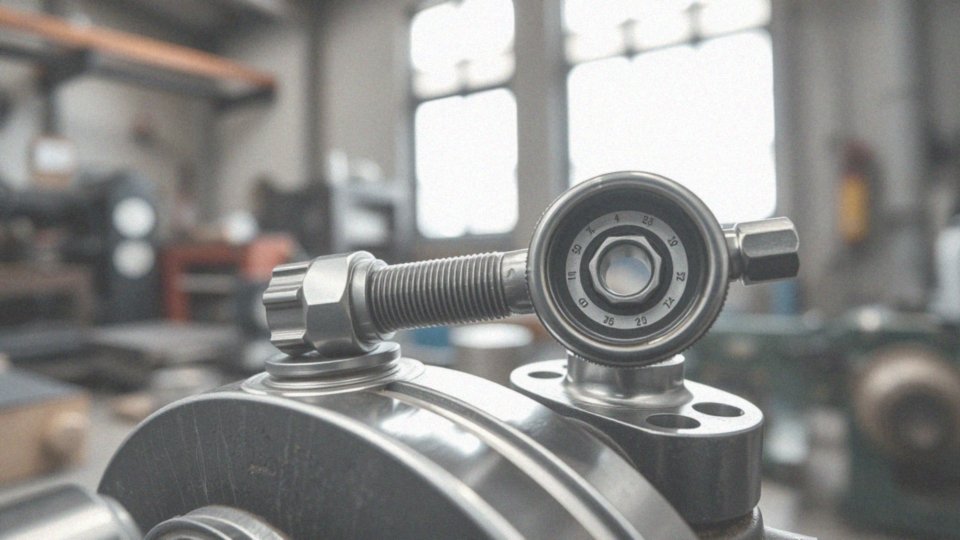
Dokręcanie śruby o 90 stopni odnosi się do obracania jej o dodatkowy kąt po osiągnięciu określonego momentu, na przykład 30 Nm. Taki manewr jest wykorzystywany w połączeniach, które wymagają dokładności i stabilności. Dodatkowe dokręcenie zwiększa napięcie wstępne, co w konsekwencji podnosi bezpieczeństwo konstrukcji oraz wytrzymałość samego połączenia.
Zastosowanie tej metody znacznie redukuje ryzyko pojawienia się:
- luzów,
- uszkodzeń.
Jest to szczególnie istotne w miejscach, gdzie niezawodność ma kluczowe znaczenie, jak na przykład w silnikach lub elementach nośnych. Dlatego inżynierowie często rekomendują taką technikę w standardowych procedurach montażowych, co sprzyja uzyskiwaniu trwałych i efektywnych połączeń. Warto również korzystać z klucza dynamometrycznego, aby precyzyjnie ustalić odpowiednią siłę dokręcania przed przystąpieniem do dodatkowego obrotu o 90 stopni.
Dlaczego dokręcanie śrub wymaga obrotu o 90 stopni?
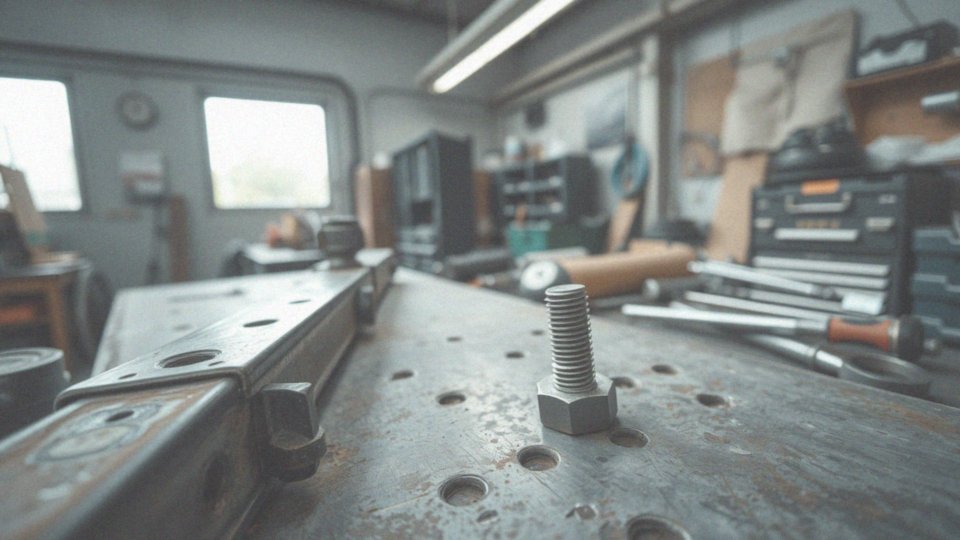
Dokręcanie śrub o dodatkowe 90 stopni po osiągnięciu ustalonego momentu obrotowego odgrywa fundamentalną rolę w inżynierii mechanicznej. Ten proces ma na celu uzyskanie odpowiedniego napięcia wstępnego, co bezpośrednio wpływa na stabilność oraz bezpieczeństwo połączenia. Dodatkowy kąt obrotu przyczynia się do optymalnego rozciągnięcia śruby, zwiększając jej siłę trzymającą.
Takie podejście do dokręcania sprzyja:
- równomiernemu rozłożeniu sił na gwincie,
- minimalizowaniu ryzyka poluzowania,
- zastosowaniom w warunkach narażonych na wibracje.
W tym kontekście klucze dynamometryczne są niezwykle przydatne, ponieważ pozwalają na precyzyjne ustawienie momentu obrotowego przed dodatkowym obrotem. Staranność w tym procesie przyczynia się do:
- wydłużenia żywotności konstrukcji,
- zwiększenia niezawodności,
- minimalizowania ryzyka istotnych awarii, szczególnie w aplikacjach montażu silników.
Wybierając metodę dokręcania, warto zwrócić uwagę zarówno na moment obrotowy, jak i dodatkowy obrót, aby zapewnić najwyższe standardy bezpieczeństwa oraz efektywności.
Jakie są zalety używania klucza dynamometrycznego przy dokręcaniu?
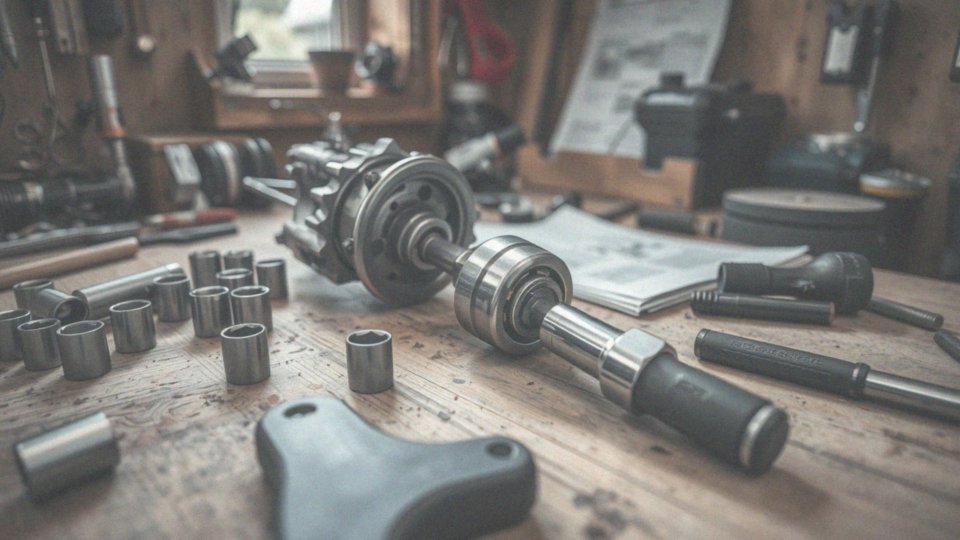
Użycie klucza dynamometrycznego oferuje wiele zalet podczas dokręcania śrub. Przede wszystkim pozwala na precyzyjne kontrolowanie momentu dokręcania, co jest kluczowe dla zapewnienia maksymalnej wytrzymałości połączeń. Taki sposób pracy znacząco redukuje ryzyko uszkodzenia elementów, takich jak:
- śruby,
- nakrętki.
Dodatkowo, klucz dynamometryczny zwiększa efektywność oraz trwałość połączeń. Wyznaczenie właściwej siły dokręcania gwarantuje, że śruby osiągną optymalny poziom, co pozwala uniknąć luzów i zachować integralność strukturalną. W inżynierii mechanicznej, zastosowanie tego narzędzia jest kluczowe dla stabilności i bezpieczeństwa konstrukcji, szczególnie w krytycznych aplikacjach. Wartością klucza dynamometrycznego jest to, że możemy dokładnie kontrolować moment dokręcania, co w dużym stopniu zwiększa niezawodność połączeń. Użytkownicy mogą być pewni, że elementy są solidnie zamocowane, co z kolei ogranicza ryzyko awarii mechanicznych. Taki sposób działania nie tylko podnosi jakość wykonania, ale także wydłuża żywotność komponentów, co przynosi oszczędności w dłuższym okresie.
Jak tarcie wpływa na moment dokręcania śrub?
Tarcie odgrywa kluczową rolę w procesie dokręcania śrub. Działa zarówno statycznie, jak i dynamicznie między gwintami śruby a nakrętką, co ma ogromny wpływ na efektywność całego połączenia. Wartość współczynnika tarcia różni się w zależności od używanych materiałów, stanu powierzchni oraz rodzaju zastosowanego smaru. Na przykład:
- śruby ze stali nierdzewnej mają inny współczynnik tarcia niż ich odpowiedniki z metalu ocynkowanego,
- w trakcie dokręcania tarcie generuje opór, który ma istotny wpływ na moment obrotowy używany w tym procesie,
- wysoka wartość tarcia oznacza, że więcej energii jest potrzebnej do przezwyciężenia tego oporu, co z kolei może prowadzić do mniej precyzyjnych pomiarów momentu dokręcania.
Inżynierowie muszą zatem brać pod uwagę współczynnik tarcia, aby osiągnąć optymalne napięcie wstępne w połączeniach. Rzetelne pomiary, które uwzględniają zarówno siłę, jak i tarcie, podkreślają znaczenie precyzyjnych narzędzi, takich jak klucze dynamometryczne. Całkowite wyeliminowanie tarcia jest niemożliwe, dlatego kluczowe staje się odpowiednie dobranie smarów i parametrów, co wpływa na trwałość oraz stabilność połączeń, szczególnie tych narażonych na duże obciążenia. Ponadto, zbyt mocne dokręcanie może prowadzić do uszkodzenia gwintów, dlatego precyzyjne pomiary są fundamentem skutecznego montażu śrub w różnych aplikacjach mechanicznych.
Jakie parametry mają wpływ na siłę dokręcania?
Dokręcanie śrub jest procesem, na który wpływa szereg istotnych czynników. Do najważniejszych należą:
- średnica śruby,
- skok gwintu,
- klasa wytrzymałości materiału,
- współczynnik tarcia,
- prawidłowe zastosowanie uszczelek i podkładek.
Średnica oraz skok gwintu decydują o potrzebnym momencie obrotowym do osiągnięcia właściwego naprężenia. Zwiększona średnica pozwala na głębsze gwintowanie, co znacząco poprawia efektywność przenoszenia momentu obrotowego. Klasa wytrzymałości materiału ma kluczowe znaczenie; na przykład, śruby z high-tensile stali są w stanie wytrzymać znacznie większe obciążenia niż ich aluminiowe odpowiedniki. W procesie dokręcania niezwykle ważny jest także współczynnik tarcia; jego wysoka wartość może sprawić, że konieczne będzie użycie większego momentu obrotowego, co w konsekwencji wpływa na precyzję dokręcania. Prawidłowe zastosowanie uszczelek i podkładek umożliwia lepsze rozkłady obciążeń, zmniejszając ryzyko występowania luzów. Staranna kontrola tych parametrów przekłada się na trwałość oraz niezawodność połączeń, co jest szczególnie istotne w przemyśle oraz motoryzacji, gdzie bezpieczeństwo i efektywność mają kluczowe znaczenie.
Jakie są optymalne klasy wytrzymałości dla śrub?
Klasy wytrzymałości śrub odgrywają kluczową rolę w zapewnieniu bezpieczeństwa i trwałości wszelkich konstrukcji. Wśród najpopularniejszych znajdziemy klasy:
- 8.8,
- 10.9,
- 12.9.
Każda z nich różni się nie tylko wytrzymałością na rozciąganie, ale i zastosowaniem. Klasa 8.8 jest idealna do ogólnych zastosowań, gdzie obciążenia są umiarkowane. Z kolei w trudniejszych warunkach, typowych dla stalowych konstrukcji czy części maszyn, lepiej sprawdzą się śruby klasy 10.9 oraz 12.9, które prezentują wyższą wytrzymałość. Wybór odpowiedniej klasy powinien opierać się na starannych obliczeniach inżynierskich oraz technicznych specyfikacjach.
Przy ich wykonywaniu istotne jest uwzględnienie zjawiska tarcia, które ma znaczący wpływ na siłę dokręcania. W przypadku połączeń narażonych na wibracje czy zmienne obciążenia, dobór klas wytrzymałości wymaga szczególnej staranności, co przyczynia się do minimalizacji ryzyka uszkodzeń oraz zapewnienia stabilności całej konstrukcji. Przyjęcie standardowych norm śrubowych znacząco ułatwia wybór potrzebnych komponentów w procesie projektowania.
Oprócz samej klasy wytrzymałości, nie można zapominać o prawidłowej sile dokręcania. Ona z kolei zapewnia optymalne napięcie w połączeniach, co jest kluczowe dla długotrwałej niezawodności montażu. Choć śruby o wyższych klasach wytrzymałości mogą wiązać się z wyższymi kosztami, ich zastosowanie w krytycznych obszarach, gdzie bezpieczeństwo i niezawodność są priorytetowe, jest absolutnie niezbędne.
Co to jest uszczelka i jakie ma znaczenie przy dokręcaniu?
Uszczelka to niezwykle istotny komponent w mechanice. Jej podstawową rolą jest utrzymanie szczelności pomiędzy dwiema powierzchniami, szczególnie podczas dokręcania śrub i nakrętek. Dzięki niej eliminujemy ryzyko wycieków płynów czy gazów. Uszczelki wytwarzane są z różnych surowców, w tym:
- gumy,
- silikonu,
- filcu,
- papieru,
- metalu,
- materiałów wulkanizowanych.
Ich elastyczność pozwala na doskonałe dopasowanie do nierówności powierzchni, co z kolei zwiększa zarówno trwałość, jak i efektywność połączeń. Odpowiedni wybór uszczelki oraz precyzyjne ustawienie momentu dokręcania mają kluczowe znaczenie. Zbyt mała siła dokręcania może sprawić, że uszczelka nie znajdzie się na właściwej pozycji, co prowadzi do przecieków. Natomiast zbyt duża siła może uszkodzić uszczelkę i zniweczyć jej funkcję. Dlatego istotne jest przestrzeganie wskazówek producentów dotyczących optymalnych wartości momentu dokręcania.
Wybór właściwego rodzaju uszczelki, na przykład metalowej lub szmacianki, ma ogromne znaczenie szczególnie w warunkach zmiennego ciśnienia lub temperatury. W silnikach oraz układach hydraulicznych szczelność wpływa na bezpieczeństwo oraz niezawodność całego systemu. Dobrze dobrana i poprawnie zamontowana uszczelka, współdziałająca z odpowiednim momentem dokręcania, gwarantuje długotrwałe oraz skuteczne funkcjonowanie połączenia.
Jakie uszkodzenia mogą wystąpić przy nieprawidłowym dokręcaniu?
Nieprawidłowe dokręcanie śrub może prowadzić do różnorodnych uszkodzeń, które mają poważne konsekwencje dla bezpieczeństwa oraz trwałości konstrukcji. Oto kilka najczęściej występujących problemów:
- Zerwanie gwintu – zbyt mocne dokręcanie może uszkodzić gwint w śrubie lub nakrętce, co sprawia, że nie da się ich ponownie wykorzystać. Statystyki wskazują, że ten problem dotyczy około 15% błędów podczas montażu.
- Deformacja elementu mocowanego – przekroczenie zalecanego momentu dokręcania może powodować trwałe odkształcenia, które wpływają na właściwości mechaniczne mocowanych komponentów i osłabiają stabilność całej konstrukcji.
- Uszkodzenie uszczelki – zbyt intensywne dokręcenie może doprowadzić do zniekształcenia uszczelki, co na dłuższą metę prowadzi do wycieków płynów lub gazów. Niewłaściwe dokręcenie przyczynia się do 20% uszkodzeń w układach hydraulicznych i silnikowych.
- Poluzowanie się połączenia – zbyt luźne dokręcenie śrub powoduje luz, który może wynikać z wibracji lub obciążeń dynamicznych. To szczególnie istotne w kontekście aplikacji przemysłowych oraz motoryzacyjnych.
- Pęknięcie śruby – w najgorszym scenariuszu może dojść do pęknięcia śruby, co stwarza poważne zagrożenie dla bezpieczeństwa. Badania dowodzą, że takie awarie mogą generować koszty napraw wynoszące nawet 30% wydatków firm.
Aby ograniczyć ryzyko wystąpienia wyżej wymienionych problemów, niezwykle istotne jest korzystanie z kluczy dynamometrycznych. Przestrzeganie zalecanych wskazówek dotyczących momentu dokręcania zapewnia odpowiednie napięcie oraz bezpieczeństwo połączeń w konstrukcjach mechanicznych.
Jak wygląda kolejność dokręcania śrub w silniku?
Kolejność dokręcania śrub w silniku, zwłaszcza w obszarze głowicy, odgrywa kluczową rolę w równomiernym rozkładzie sił oraz zapobieganiu deformacjom. Proces zazwyczaj zaczyna się od śrub znajdujących się w centrum, a następnie przechodzi do tych umieszczonych na obrzeżach. Ważne jest, aby dokręcanie przebiegało w sposób krzyżowy, co pozwala na jednorodne napięcie uszczelki.
Szczegółowe wskazówki dotyczące kolejności dokręcania można znaleźć w instrukcji serwisowej danego silnika. Ich przestrzeganie jest kluczowe dla zminimalizowania ryzyka awarii.
W przypadku silników czterosuwowych często stosuje się numerowaną procedurę, która zapewnia równy moment dokręcania dla wszystkich śrub, co z kolei wpływa na stabilność całej konstrukcji. Co więcej, istotne jest przy tym zwrócenie uwagi na właściwe ustawienie momentu dokręcania:
- zbyt mały moment może prowadzić do luzów,
- zbyt wysoki ma potencjał uszkodzenia gwintów lub deformacji elementów.
Precyzja w trakcie dokręcania jest więc niezwykle istotna dla długowieczności oraz efektywności silnika. Ostatecznie, odpowiednio dokręcone śruby mają bezpośredni wpływ na bezpieczeństwo i skuteczność całej jednostki napędowej.
Jakie są etapy dokręcania głowicy silnika?
Dokręcanie głowicy silnika to proces, który wymaga szczególnej uwagi, składający się z kilku istotnych etapów. Jego głównym celem jest zapewnienie odpowiedniego napięcia oraz zminimalizowanie możliwości deformacji. Cała procedura rozpoczyna się od wstępnego dokręcenia wszystkich śrub na niewielki moment, na przykład 20 Nm. Następnie moment zwiększa się stopniowo, osiągając 40 Nm, a potem 60 Nm, zgodnie z zaleceniami producenta.
Gdy śruby osiągną wymagany poziom dokręcenia, ważne jest wykonanie dodatkowego obrotu o 90 stopni. Ten krok istotnie zwiększa napięcie wstępne, co jest kluczowe dla trwałych i stabilnych połączeń. Podczas dokręcania głowicy niezwykle ważna jest także kolejność działania. Przestrzeganie ustalonej sekwencji pozwala na równomierne rozłożenie sił, co z kolei minimalizuje ryzyko uszkodzenia.
Dodatkowo, przy każdej wymianie głowicy, wskazana jest wymiana śrub. To zapobiega osłabieniu ich struktury, które mogłoby powstać w wyniku wcześniejszego używania. Dbałość o każdy z etapów dokręcania przekłada się na dłuższą żywotność jednostki napędowej oraz znacząco obniża ryzyko poważnych awarii.